Streamlining ISO Compliance: How Technology Can Simplify Your Cement Industry Processes
When you’re formulating a new cement-based product, or reformulating an existing one, you’re aiming to ensure it meets all internal and external standards. This isn’t always easy, especially if time and resources are limited.
The solution is having access to the most appropriate technology. As well as the technical expertise to use it to maximum effect.
This doesn’t have to mean buying the equipment yourself. Because some cement-based product manufacturers invest heavily in technology and resource expertise. This will help your customers remain compliant without slowing product development or taking up too much time.
What does this look like? Read on to find out.
Step 1 – your compliance end goals mark the starting point
Experienced construction chemical suppliers start with a clear understanding of the three sets of compliance requirements your cementitious products need to meet. For example:
1. Your internal product standards
Typically this means adhering to internal policies and procedures like ISO9001 to maintain quality throughout your change management process as well as meeting your performance, cost, sustainability, health and safety and environmental standards.
2. External standards and regulations
Ensuring any product formulation meets the requirements of whichever national or international standard it’s designed to meet.
3. Product liability insurance standards
Making sure your product meets the liability insurance standards so your new application is covered.
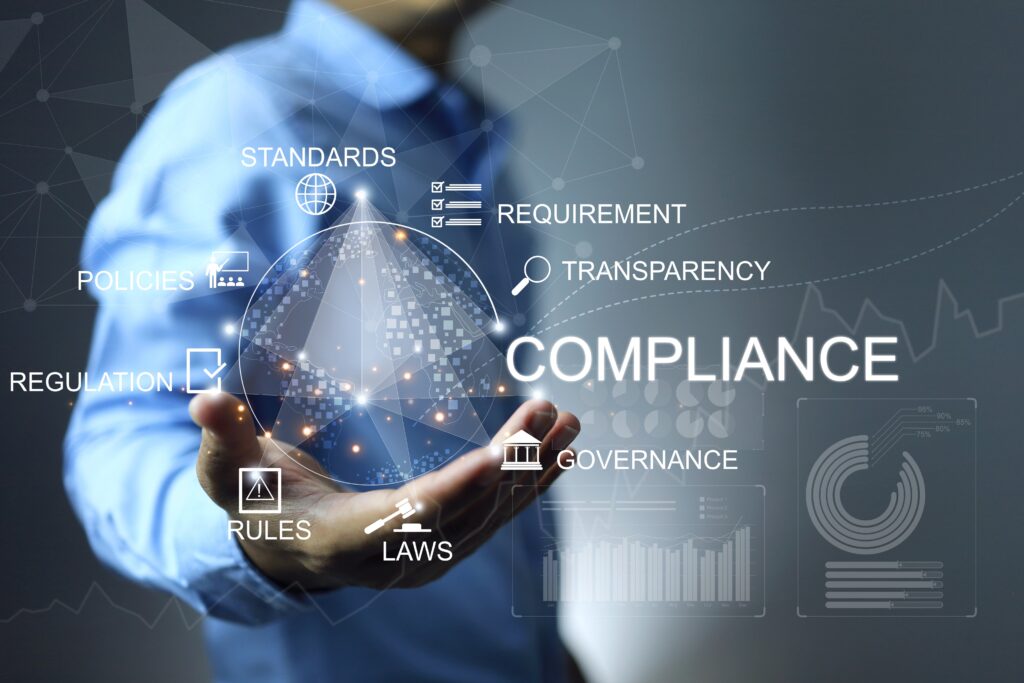
Step 2 – the right tests are established or new ones created
A detailed understanding of this backdrop sets the direction for the types of testing that need to be carried out and the equipment to do this. Even if specific testing methods don’t exist, a leading supplier will use their expertise to create robust new test methodologies that will provide peace of mind. As well as helping shape future product standards to ensure the products’ relevance to the industry.
Step 3 – high-quality testing is carried out giving you peace of mind
The equipment needed will vary depending on the cementitious product you’re developing and the regulations and standards governing its use. Here are two examples of the types of equipment that will not only ensure you remain compliant but bring the potential to enhance your formulation – or reduce its cost – too.
Scenario 1 – replacing the cement in a cement-based tile adhesive
A traditional fast-setting, cement-based tile adhesive can be reformulated to remove a significant percentage of the ordinary Portland cement (OPC) from the formulation. An OPC-free binder system can also be used.
It’s key to ensure these binder systems are still able to meet the relevant industry standard and work consistently in the market. Standard testing equipment – like auto vicats and adhesion strength testers – are essential in ensuring the end product is fit for purpose. But, the end formulation can be improved further by combining these methods with ultrasonic hydration monitoring. Giving increased confidence in the development pathway being followed.
This is highly relevant when creating a formulation that uses a lower-carbon-based binder system. Ensuring these types of binder systems provide early strength development, for example in a rapid-setting tile adhesive, is key to increasing sustainability while maintaining product performance.
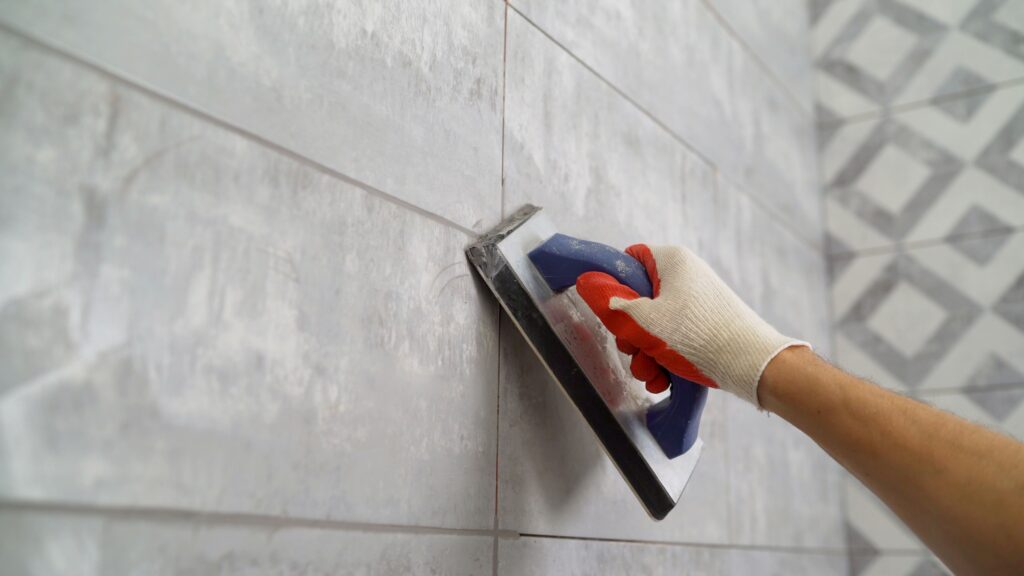
Scenario 2 – ensuring a guaranteed 12-month shelf life for a product containing chromium-6
EU and UK law dictates any product containing Portland cement must have a chromium-6 content of below two parts per million for the duration of its stated shelf life. High-quality testing is vital to ensuring your product meets these specifications.
Ideally, you’ll test your formulation using accelerated storage techniques that synthesise storage to ensure shelf-life stability. To do this, look out for a company with a UV-based spectrophotometer, the relevant reagents and the expertise to use this specialist equipment.
With the right technical expertise, this piece of kit can help enhance the robustness of a product’s shelf-life. Giving confidence that the end product will meet the stated shelf-life requirements. The testing could also reveal the option to use lower doses without impacting its stability, potentially resulting in a more cost-effective product.
How can you apply these kinds of technologies without breaking the bank?
Buying all this kit can be expensive, particularly if you’re not going to use it too often. The alternative is to look out for an additive supplier that invests in a wide range of tech across multiple construction chemical industry product types. Providing you with advanced testing capability that can be trusted across screeds, self-levelling underlays, renders, technical mortars, tile adhesives and more.
Cutting-edge tech is key to helping you rapidly reformulate your products so they meet or beat your performance requirements as well as the relevant regulatory and compliance standards.
To find out if Cemkem could be your next construction chemical partner, get in touch with one of our talented technical team on 0161 762 0044 or at sales@cemkem.co.uk.